Ultrasonic cleaning: educational program for tattoo artists
Helping the Permanent Makeup Artist
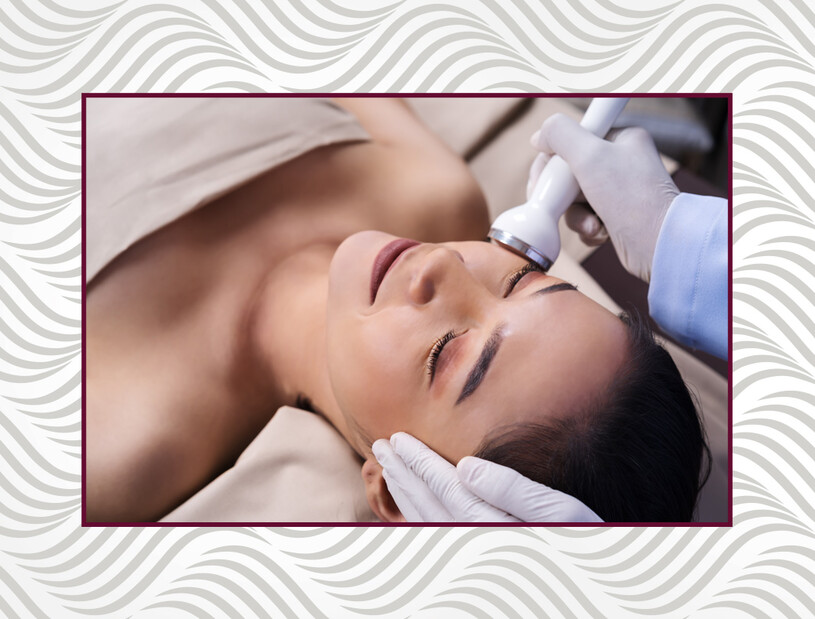
What is ultrasonic cleaning of objects and what needs to be done for this? What is the effect of cavitation? What liquid can be used for ultrasonic cleaning? All these questions are answered in the article.
Ultrasonic cleaning is a method of cleaning the surface of solids in washing liquids, in which ultrasonic vibrations are introduced into the liquid in one way or another. The use of ultrasound usually significantly speeds up the cleaning process and improves its quality. In addition, in many cases it is possible to replace flammable and toxic solvents with safer detergents without compromising cleaning quality. Ultrasonic cleaning is used in many industries, in the repair of machines and mechanisms, in jewelry and restoration, in medicine, etc.
Cleaning occurs due to the combined action of various non-linear effects that occur in the liquid under the action of powerful ultrasonic vibrations. These effects are: cavitation, acoustic currents, sound pressure, sound-capillary effect, of which cavitation plays a decisive role. Cavitation bubbles, pulsating and collapsing near pollution, destroy them. This effect is known as cavitation erosion. For ultrasonic cleaning, the correct choice of cleaning solution is important so that it effectively dissolves or emulsifies contaminants, while at the same time not affecting the surface being cleaned as much as possible. The latter circumstance is especially important, since ultrasound usually significantly accelerates physical and chemical processes in liquids, and an aggressive detergent can quickly damage the surface. Ultrasonic cleaning should not be used when the cavitation resistance of the surface to be cleaned is less than the contamination resistance. For example, when removing sticky films from aluminum parts, the probability of destruction of the parts themselves is high. It should be remembered from the 7th grade chemistry lesson that aluminum interacts with water, releasing hydrogen and aluminum hydroxide. It is protected by an oxide film, which can be easily destroyed. The optimal concentration of the working solution is selected experimentally. When cleaning high-alloy steels, washing in distilled water is desirable. Washing with a weak solution of citric acid is recommended to neutralize alkaline residues. The concentration of the working solution and the washing solution is adjusted with an ionometer (pH meter) or litmus paper.
Pollution and effects on them
From the point of view of ultrasonic cleaning, contamination is distinguished by three signs:
1. Cavitation resistance, that is, the ability to withstand microshock loads.
2. Strength of bond with the surface to be cleaned, resistance to peeling.
3. The degree of interaction with the washing liquid, that is, whether and how capable this liquid is of dissolving or emulsifying pollution.
Cavitation resistant contaminants lend themselves well to ultrasonic cleaning only if they are weakly bound to the surface or interact with the cleaning solution. These are fatty contaminants that are well washed in slightly alkaline solutions. Lacquer or paint coatings, scale, oxide films are usually cavitation resistant and well bonded to the surface. For ultrasonic cleaning of such contaminants, rather aggressive solutions are needed, because here only the third of the listed signs can act. Cavitationally unstable contaminants (dust, porous organics, corrosion products) are relatively easy to remove even without the use of special solutions.
In ultrasonic cleaning, both plain water and aqueous solutions of detergents and organic solvents are used as a washing liquid. The choice of agent is determined by the type of contamination and the properties of the surface to be cleaned (see above).
Ultrasonic cleaning devices
Ultrasonic cleaning requires a container with a cleaning solution and a source of mechanical vibrations of ultrasonic frequency, called an ultrasonic emitter. The surface of the ultrasonic transducer, the body of the container, and even the part to be cleaned can act as an emitter. In the latter cases, the ultrasonic transducer is attached, respectively, to the body or to the workpiece. An ultrasonic transducer converts the electrical vibrations applied to it into mechanical vibrations of the same frequency. Most installations use frequencies from 18 to 44 kHz with an oscillation intensity of 0.5 to 10 W/cm. The upper limit of the frequency range is due to the mechanism of formation and destruction of cavitation bubbles: at a very high frequency, the bubbles do not have time to collapse, which reduces the microshock effect of cavitation. Transducers can be magnetostrictive or piezoceramic. The former are distinguished by their large size and weight, significantly lower efficiency, however, they allow reaching high power, on the order of several kilowatts. Piezoceramic transducers are more compact, lighter, more economical, but their power, as a rule, is not so great - up to several hundred watts. Such power, however, is sufficient for the vast majority of applications, given that in large installations several emitters are used at once.
The best known devices are ultrasonic baths, units specially designed for ultrasonic cleaning. Transducers in such baths, as a rule, are either built into holes in the case, or attached to the case, making it a radiator, or placed inside as separate modules. Each method has its own advantages and disadvantages. Separate modules of ultrasonic transducers (emitters) can be built into production lines where fast and high-quality cleaning is required. So, for example, they do it for continuous cleaning of rolled metal and wire at different stages of their production and use. Known transducers are made in the form of small hand tools for precise cleaning of complex surfaces. For cleaning printed circuit boards used in radio electronics, the best performance (obtained experimentally) has a solution of popular detergents and water. When cleaning in special baths, it is desirable to heat the solution to a temperature of + 25-40 degrees Celsius throughout the entire process.
Ultrasonic cleaning is a method of cleaning the surface of solids, based on the excitation of ultrasonic frequency oscillations in a washing solution. The scientific basis for the creation of equipment and the development of ultrasonic cleaning technology was laid by the work in the field of acoustic cavitation, carried out at the "Acoustic Institute named after Academician N.N. Andreev" under the guidance of Professor L.D. Rozenberg. Ultrasonic cleaning allows you to replace manual labor, thereby speeding up the cleaning process, to obtain a high degree of surface cleanliness, and virtually eliminate the use of flammable and toxic solvents.
The process of ultrasonic cleaning is caused by a number of phenomena that occur in a high-intensity ultrasonic field: acoustic cavitation, acoustic currents, radiation pressure, sound-capillary effect. Studies have shown that, depending on the type of pollution, various processes play a predominant role in cleaning. Thus, the destruction of weakly interconnected contaminants occurs mainly under the action of pulsating (non-collapsing) cavitation bubbles. At the edges of the film of contamination, pulsating bubbles, making intense vibrations, overcome the forces of adhesion of the film to the surface, penetrate under the film, break it and peel it off. Radiation pressure and sound-capillary effect contribute to the penetration of the cleaning solution into micropores, irregularities and blind channels.
Acoustic currents carry out accelerated removal of contaminants from the surface. If the contaminants are firmly attached to the surface, then for their destruction and removal from the surface, the presence of collapsing cavitation bubbles is necessary, creating a microshock effect on the surface. To implement the required mode of ultrasonic cleaning, it is necessary to choose the optimal values of the ultrasound intensity and oscillation frequency. With increasing frequency, the cavitation bubble does not reach the final stage of collapse, which reduces the microshock effect of cavitation. Excessive lowering of the frequency leads to an increase in the level of airborne noise, and requires an increase in the dimensions of the radiator. Therefore, most industrial installations operate in the range of 18-44 kilohertz. An increase in the intensity of ultrasound above a certain limit leads to an increase in the amplitude value of the pressure, and the cavitation bubble degenerates into a pulsating one. At low intensity values, cavitation and all secondary effects that occur in the liquid when ultrasonic vibrations are introduced and determine the cleaning efficiency are weakly expressed. The working range of intensity is 0.5-10 W/cm2. An important role in the cleaning process is played by the correctly selected composition of the washing liquid. In this case, it is necessary to take into account the material properties of the part to be cleaned and the type of contamination. The washing liquid should enter into chemical interaction only with surface contaminants, but not with the material of the product to be cleaned. The physical and chemical properties of the liquid have a significant influence on the course and development of specific phenomena excited by ultrasound in washing solutions. Increasing the vapor pressure inside the bubble sharply reduces the intensity of cavitation, therefore, for example, the use of aqueous solutions for ultrasonic cleaning is more efficient than the use of organic solvents. Currently, special baths are used as ultrasonic cleaning devices. It should be remembered that it is strictly forbidden to use flammable and explosive substances as a cleaning solution!
Read also